The RGM2-201F is a gas analyzer for CVD, etching, and ALD applications. Moreover, its purpose is to reduce the size of the system.
In sputter equipment, process control using a gas analyzer is common. However, ULVAC said, “It is difficult to introduce large-scale equipment on CVD and etching production lines, which are even more difficult to process, and gas analysis has not been performed.”
The new gas analyzer is one of the world’s smallest products for CVD and etching equipment. In addition, the minimization of the footprint was made possible by the integration of the exhaust system and the control system.
Fosters Production Efficiency
The two systems had been separated, but the company was the first to adopt an integrated type. Another major feature is that it can be placed vertically. In the case of vertical installation, it achieves up to 40% space savings compared to competing products.
Furthermore, another major improvement is the product’s easy maintenance feature.
The filament, which heats to 1200~1400°C and emits thermal electrons, wears out easily. Thus, breaking out eventually.
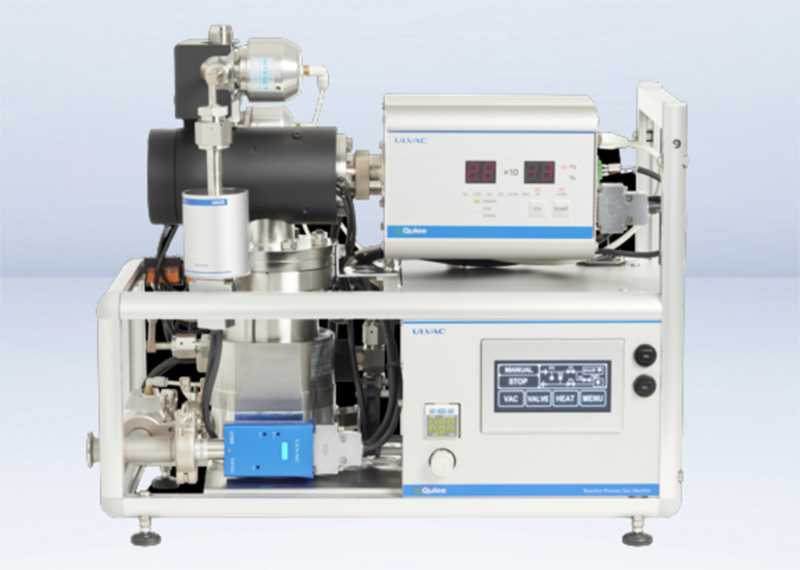
By changing the direction of gas inflow in the RGM2-201F, workability has been improved, such as reducing the time and effort required to remove the valve, which was a heavy burden.
In the past, it took about two hours for two workers to perform the replacement work. Currently, however, one worker can do it in about 10 minutes. A series of systems that dramatically improve maintainability are patent pending.
The fluorine-based toxic gas used in CVD and etching is also burdensome for filaments, and the frequency of filament replacement is higher than that of sputtering equipment. It was the first gas analyzer for CVD and etching equipment to adopt a method of mounting two filaments. Thus, succeeding in reducing the frequency of replacement.
ULVAC emphasizes the reduction of downtime by equipping alternative filaments for process management on semiconductor and electronic component production lines. Until now, if the filament ran out, the product in the middle of production would be treated as a defective product, resulting in a large loss, but with the spare filament, measurement can be continued without stopping the production line.
Expands Role of Gas Analyzers
There are many advantages to adopting an ion source method that other companies do not have. That is, a closed ion source with a V-shaped magnet. The thermal electrons coming out of the filament collide with the gas on the device side to ionize, but in this method, the heat electrons rotate in a spiral with the force of the magnetic field of the magnet. Compared to the type that does not use magnets, the probability of collision with the gas increases, and the amount of ion molecules transferred to the filter section that separates the mass increases, resulting in highly sensitive gas analysis.
While keeping the “emission current” applied to the filament about one order of magnitude lower than that of other companies’ devices, the sensitivity has been improved by about 50%.
The reduced load also led to a longer filament life. The improved sensitivity eliminates the need for expensive consumable amplifiers (secondary electron multiplier tubes), reducing running costs.
Among the major features of the RGM2-201F are its compact size, high sensitivity, and easy maintenance. For that reason, the company hopes to encourage the introduction of gas analyzers in CVD and etching processes.
Repost: ASIA ELECTRONICS INDUSTRY